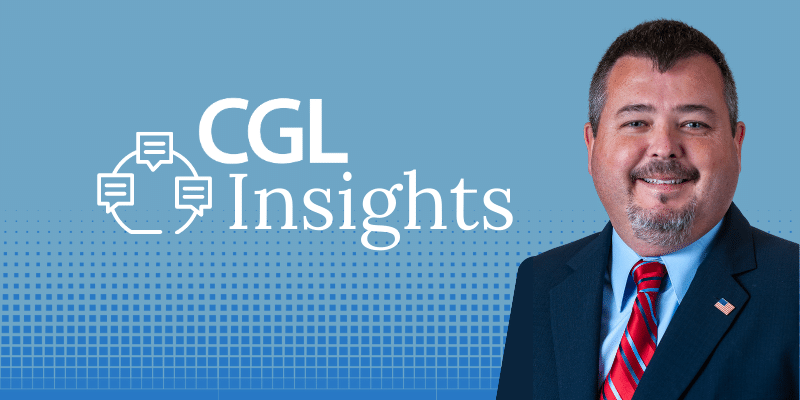
How Does Your FM Program Stack Up? A 5-Step Process for Assessing the Performance of Your Facility Maintenance Program
Facility maintenance is essential to ensure the smooth functioning of any facility, whether it is a detention or correctional facility, courthouse, or any other commercial building. Preventative and predictive maintenance are two key strategies that can help facility managers to maintain their facilities in good condition and avoid costly breakdowns or repairs.
Assessing the performance of a facility maintenance program is critical to determine whether it is meeting its objectives and to identify areas where improvements can be made. Below, I’ve outlined a simple six-step process that will help you assess the performance of your facility maintenance program with an emphasis on preventative and predictive maintenance:
STEP 1: Define Key Performance Indicators (KPIs)
The first step in assessing the performance of a facility maintenance program is to define the key performance indicators (KPIs) that will be used to measure its effectiveness. These KPIs will depend on the goals of the maintenance program. Still, they may include metrics such as:
- Response time to maintenance requests (by category, i.e., plumbing, electrical, or HVAC…)
- Percentage of scheduled maintenance completed on time
- Breakdown of preventative maintenance and corrective maintenance (total number and ratio)
- Total time to correct
- Employee utilization
STEP 2: Collect Accurate, Reliable Data
Once the KPIs have been defined, the next step is to collect data on each of these metrics. This can be done through various means, such as computerized maintenance management systems (CMMS), other work order systems, equipment monitoring systems, and surveys of facility users. It is essential to ensure that the data collected is accurate and reliable, as this will form the basis of the assessment.
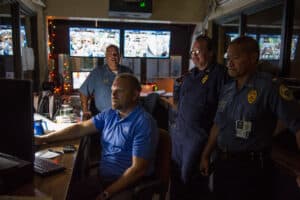
Deploying a CMMS is a great way to continually monitor progress towards your facility maintenance goals. Proper training for staff will ensure quality data is input and future results are accurate.
STEP 3: Analyze the Data & Identify Areas for Improvement
Once the data has been collected, it is essential to identify trends and patterns. This can be done using various analytical tools like spreadsheets, pivot tables, charts, and graphs. The analysis should focus on identifying areas where the facility maintenance program is performing well and areas with room for improvement, your program’s “weak spots.”
Defining your program’s weak spots may involve identifying equipment that requires more frequent maintenance, improving response times to maintenance requests, or increasing the percentage of scheduled maintenance completed.
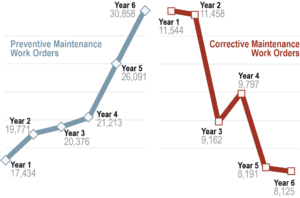
In this sample analysis, you can see as preventative maintenance increased, corrective maintenance work orders decreased.
STEP 4: Define Your Goals & Develop an Action Plan
What goals do you have for each underperforming area? Is it to improve average response times by “X” hours? Or maybe it’s to increase the percentage of scheduled maintenance completed by “X” percent? Whatever your goals are, they should be clearly communicated in your action plan.
Once areas for improvement have been identified and goals have been established, developing an action plan to address those issues and reach your goals is essential. Strategies in your plan may include implementing new maintenance procedures, investing in new equipment, or hiring additional staff. Remember that each action plan is unique to your program or facility and should be based on the data you collected, analyzed, and designed to address the areas where the facility maintenance program is underperforming.
STEP 5: Monitor Progress
Finally, monitoring progress toward the goals set out in the action plan is essential. This can be done through regular reporting and analysis of KPIs and ongoing feedback from facility users and maintenance staff. The monitoring process should ensure that the facility maintenance program continues to improve over time and that any issues are identified and addressed promptly.
In conclusion, assessing the performance of a facility maintenance program with an emphasis on preventative and predictive maintenance requires a systematic approach that involves defining KPIs, collecting and analyzing data, identifying areas for improvement, defining goals, developing an action plan and monitoring progress. Following this process will help facility managers ensure that their facilities are well-maintained and give them greater control over maintenance costs.
About the Author:
Russ Rieske is a talented Engineering Manager with demonstrated experience working in more than 40 justice facilities across the United States where he has managed complex projects and led multiple cross-functional teams to successful outcomes. Highly skilled in Facility Management (FM), Logistics Management and Mechanical Engineering, Russ is a strong information technology professional with extensive experience in database management and computer maintenance management systems. He has a Bachelor of Science (B.S.) degree focused in Aerospace Engineering, Mechanical Engineering and Mathematics from the Georgia Institute of Technology.
Connect with Russ on LinkedIn