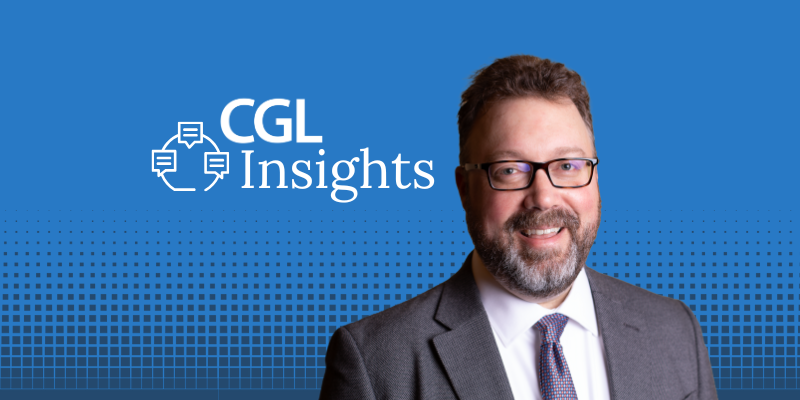
Modular Cells 101: The Practical Integration of Precast Concrete Cells in Correctional and Detention Facility Construction
In our first blog post, we introduced you to the concept of modular precast concrete cells, highlighting their benefits in speed, security, cost-efficiency, and durability. We also discussed the different types of modules available and the potential challenges they bring. Now, let’s dive deeper into how to effectively integrate these modules into your construction projects. In this second post, we will explore the critical considerations for incorporating modular precast concrete cells, best practices for manufacturing, and the logistics required to ensure a smooth process from design to installation.
Let’s walk through how to manage the integration of precast concrete cells at each stage of the project lifecycle—ensuring a streamlined process that delivers the benefits promised by this innovative construction method.
Project Integration: Bringing Precast Modules to Life
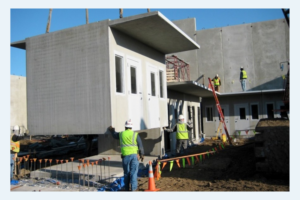
Setting modules with precision during early-stage integration ensures a strong start to the overall construction timeline.
The integration of precast concrete modules into a construction project isn’t just about choosing a method of construction; it’s about planning and executing every stage to ensure that the modules meet the design requirements and are installed efficiently. Proper planning, coordination, and best practices can maximize the benefits of using precast concrete systems.
1. Schematic Design Phase: Early Coordination
In the schematic design phase, the project layout should be assessed for compatibility with precast concrete modules. While the design might still be in its infancy, reaching out to manufacturers early helps inform the direction of the design. Manufacturers can offer preliminary layouts, budget estimates, and important design feedback. Early manufacturer involvement helps identify potential issues before they become costly problems and ensures that the final design is optimized for precast construction.
2. Design Development Phase: Aligning Design and Manufacturing
Once precast modules are confirmed as the construction method of choice, it is crucial to refine the design to align with the manufacturer’s capabilities. Each precast manufacturer may use different molds, production processes, and materials, so it’s essential that the design accommodates these variables. During this phase, the design should be adjusted to allow for flexibility in module configurations, maximizing the use of existing molds and minimizing additional costs for custom designs.
At this point, manufacturers can also provide updated budgetary feedback as the design becomes more specific, ensuring the project stays within financial constraints.
3. Bid Phase: Preparing for a Competitive Process
During the bid phase, it’s critical for the general contractor to evaluate multiple manufacturers’ bids, not just for cost but also based on their production capabilities and methods. Manufacturers will have different strengths, so understanding their processes—whether for off-site or on-site production—is key. This evaluation should also consider how site preparation needs (such as space for casting, equipment requirements, etc.) will impact the overall project budget.
4. Coordination Phase: Streamlining Production and Site Work
The coordination phase is vital for keeping the project on track. Precast module production often begins before site work is completed, which means early and constant communication between the design team, general contractor, trade subcontractors, and manufacturer is necessary. Ensuring that the manufacturer has all the needed information ahead of time helps prevent delays. Coordination of the delivery and installation schedule is also crucial to keep the project timeline intact.
5. Construction Phase: Delivery, Storage, and Installation
Once precast modules are ready for installation, it’s essential to ensure there is ample space on the site for staging and for crane access. The modules, whether manufactured on-site or off-site, must be stored carefully to avoid damage before installation. For off-site production, transportation logistics are a major consideration, with heavy modules requiring specialized transport methods, including permits for road travel.
Once the modules arrive on-site, the installation process begins. Cranes and lifting equipment will be required to move the modules into place. To minimize delays, staging areas should be set up ahead of time so that modules are ready for quick installation. The success of the installation phase depends on efficient module delivery and precise execution of the erection plan.
Best Practices for Successful Precast Concrete Module Integration
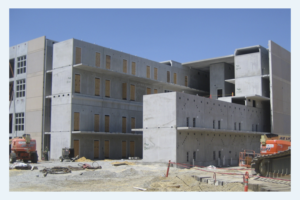
Site accessibility and proper staging support the smooth delivery and placement of precast modules.
1. Effective Site Planning and Access
Whether modules are manufactured on-site or off-site, site planning is crucial. The site must accommodate both casting equipment (if on-site) and staging areas for the modules before they are installed. If modules are being cast off-site, logistics around transportation, storage, and crane access become the main considerations.
For on-site manufacturing, ensure that sufficient space is available for the entire production process, from casting to storing and moving modules. Proper access roads for cranes, trucks, and other heavy equipment are essential for the smooth flow of operations.
2. Understanding and Managing Module Types
There are various precast module types, each with different benefits and limitations. These include:
- Front Chase Modules: These modules include cells and an integral mechanical chase, ideal for larger facilities. They are often used for state and federal facilities, where large, campus-style layouts are typical.
- Rear Chase Modules: These modules are used primarily in county facilities where multiple housing types are needed under one roof. The rear chase design allows for easy access to mechanical systems.
- Dormitory Modules: Larger than standard cells, dormitory modules can house multiple inmates and often come in a rear chase configuration.
- Mechanical Plenums: These horizontal chase modules are essential in multi-level structures, where space for mechanical and electrical systems is needed between floors or at the top of mezzanine levels.
Choosing the right module type for your facility will depend on factors like the facility’s size, the layout, and its mechanical requirements. Consideration of the specific needs of each area in the facility will help ensure that the chosen module configuration supports the design and operational goals.
3. Quality Control and Inspection Standards
Rigorous quality control is essential at every stage of the precast module production process:
- Pre-pour Inspection: Before the concrete is poured into the molds, an inspection of the mold, reinforcement cage, and placement of cast-in items should be performed. This helps ensure that everything is in place for a successful casting.
- Post-pour Inspection: After the modules are poured and set, they should be inspected to confirm that there are no voids, cracks, or misalignments. Dimensional accuracy and adherence to design specifications should be checked thoroughly.
- Final Inspection: Before the modules are transported to the site, a final inspection ensures that all components are properly installed and functioning as required.
These inspections help catch any issues before the modules are shipped or installed, saving time and costs on rework later.
4. Installation and Erection Best Practices
Effective installation and module erection are critical for the long-term performance of the structure. Best practices for installation include:
- Ensuring that the crane and lifting equipment are properly sized for the modules.
- Setting up an efficient installation schedule to minimize downtime and delays.
- Protecting the modules from damage during transportation and installation.
- Using proper techniques to shim and grout modules once installed to ensure structural stability.
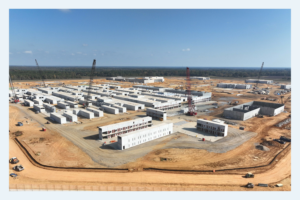
Cranes, logistics, and sequencing come together to ensure efficient, error-free installation at scale.
Carefully following the installation plan, and ensuring that every detail is executed correctly, will help avoid costly mistakes and delays.
Best Practices – Manufacturing: Ensuring Consistency and Quality
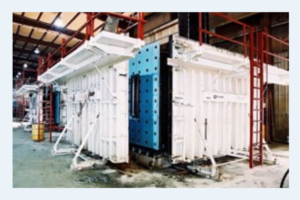
A controlled manufacturing environment supports quality and consistency across all precast modules.
The manufacturing process for precast concrete cells is highly structured, requiring precise coordination of several key stages to ensure a consistent and high-quality product. Here are the essential best practices for manufacturing precast modules:
1. Concrete Casting Area Setup
The casting area should be level and smooth to ensure that molds are mounted accurately, which is critical for maintaining tight tolerances. A separate area should be designated for assembling the steel reinforcement cages before they are placed in the molds.
2. Reinforcement Cage Assembly
Each day, a new reinforcement cage is assembled for each mold that is scheduled for casting. The cage must be assembled on a jig to ensure precise placement of the steel reinforcement. This process may include attaching electrical boxes and other fixtures to the cage to ensure proper placement during the casting process.
Before moving the cage into the mold, a quality control check should be performed to verify that all components are in the correct position.
3. Mold Setup
The mold must be cleaned and prepared each day before casting. The mold should be sprayed with a release agent to ensure that the finished module can be easily removed once the concrete has cured. Steel reinforcement and cast-in components like door frames, electrical boxes, and insulation should be placed in the mold with care, and all parts must be properly secured to prevent movement during the pour.
4. Pre-Pour Inspection
Before pouring, a thorough inspection should be conducted to ensure that the mold dimensions are correct, that reinforcement is properly placed, and that all cast-in components are securely positioned. This step is crucial for avoiding defects in the final product.
5. Pouring and Curing the Concrete
Once the inspection is complete, the concrete is poured into the mold. Self-consolidating concrete (SCC) is preferred as it fills the mold completely without the need for excessive vibration. After the pour, the modules must be cured properly to allow the concrete to achieve its full strength. During curing, care must be taken to maintain proper temperature and moisture levels to prevent cracks or other issues.
6. Post-Pour Inspection
After the concrete has cured, the modules are removed from the molds and inspected for quality. This inspection checks for any cracks, voids, or other imperfections in the finished product. Any defects should be addressed before the modules are shipped for installation.
7. Final Finish and Outfitting
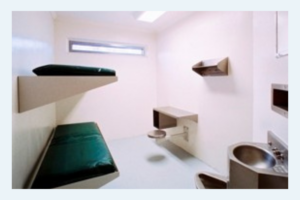
Fully outfitted modules, complete with furnishings and fixtures, are ready for transport and installation.
Once the modules are cured and inspected, they are moved to a finishing area where they receive a final coat of paint and are outfitted with fixtures such as doors, windows, and plumbing. All cast-in components are secured and checked for proper functionality before the modules are stored or transported to the site.
Manufacturer Considerations

Manufacturer setup and quality standards directly impact cost, logistics, and project outcomes.
When selecting a manufacturer for precast concrete cells, several factors should be considered to ensure the best possible outcome for your project:
1. Location
The proximity of the manufacturer to the project site plays a significant role in cost and logistics. Modules produced off-site will incur transportation costs, and long distances may lead to delays. Manufacturers located near the project site can reduce transportation costs and simplify logistics, while on-site manufacturers require substantial upfront investment in casting equipment but may be more cost-effective for large projects with significant quantities.
2. Experience and Specifications
Choose a manufacturer with a proven track record of successful projects, particularly in correctional facility construction. They should have the necessary testing data to meet required impact testing standards and be enrolled in a precast industry plant certification program such as PCI (Precast Concrete Institute). This certification ensures that the manufacturer adheres to industry standards for quality control and production practices.
3. Financial Security
It’s essential that the manufacturer can provide a performance and payment bond to guarantee the completion of the project. This bond helps protect the project owner in case of unforeseen issues or delays.
Wrapping Up: Key Tenants of Successful Precast Concrete Module Integration
Precast concrete modules offer numerous advantages for correctional facility construction, including speed, durability, cost-efficiency, and security. By carefully managing the integration of these modules into your project—from design through to installation—your facility can benefit from the strength and flexibility these modules provide.
Effective project planning, coordination, and strict adherence to best practices for manufacturing, inspection, and installation are essential for ensuring a successful outcome. By following these guidelines, you can avoid common pitfalls and maximize the value of your modular precast system.
Considering precast concrete cells for your next correctional facility? There are knowledgeable resources and partners available to guide you through every step of the process.