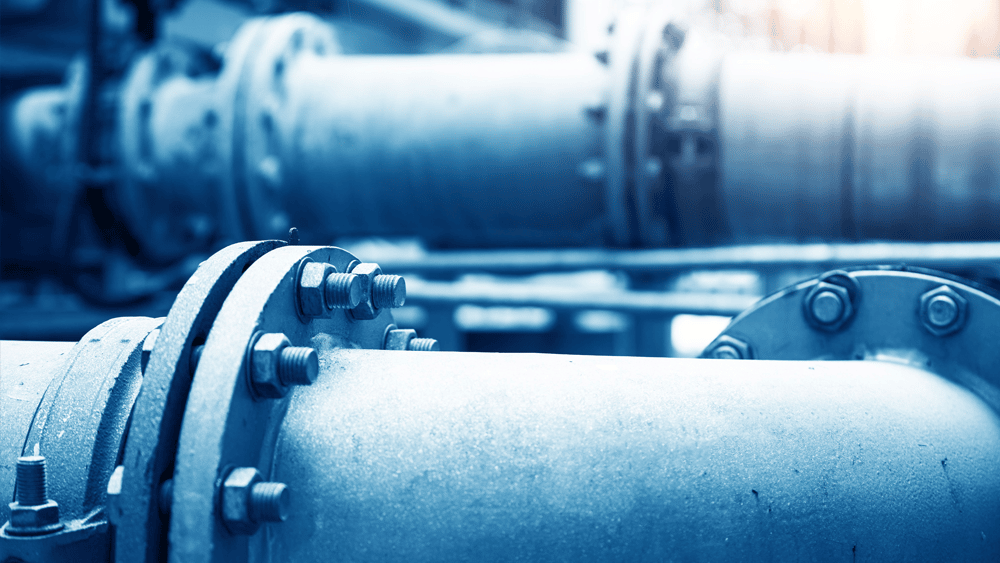
Early Maintenance Can Mean Lower Long-Term Facility Costs
Your agency is planning to build a new facility — or maybe it’s a renovation of administrative space or the addition of a housing unit. Whatever it may be, you have the chance to build something new. At what point during the design process should you involve maintenance personnel to consider longterm life cycle implications?
The answer: as early as possible if you want to affect operating costs and save money.
Getting maintenance professionals involved with design can have a positive impact on cost savings, including: reducing annual operating costs and lowering long-term facility costs.
Reducing Operating Costs
Justifying an annual budget can be difficult, especially because of year-to-year changes. However, when maintenance experts have input into the design process, some budget-line items can become more stable. For example, specifying more durable, easy-to-maintain materials (where appropriate) can avoid repair and replacement costs without sacrificing aesthetics. Personnel familiar with day-to-day operations may also be able to make suggestions on implementing energy savings with which designers aren’t familiar.
Savings Over the Building’s Life
Reducing annual costs obviously builds up savings over the life of your new facility. It may also be possible to design the facility, which may not lower the cost of construction but will lower the long-term life cycle cost because of efficiencies or operational advantages.
Take, for example, CGL’s involvement with Forsyth County, Ga. CGL helped deliver a new justice campus for the county by serving as the program manager/owner’s representative. The project budget for the new Forsyth County Courthouse and Justice Center was $100 million, but that’s just the beginning of the story. Over the life of the two buildings, Forsyth County was projected to spend more than $2 million per year on average for operations, above and beyond the project budget. These costs included correctional officers, utilities, maintenance and repairs as well as long-term costs like upgrades and renovations. The county knew, from the outset of the project, that it needed to find savings where possible to sustain its justice operations.
CGL made sure county maintenance personnel were included as consultants during design. Their input ensured county infrastructure requirements were met so that there would be a commonality of materials and procedures. This gave the county the ability to save on purchasing costs and allowed contractors to take advantage of volume discounts available to the county. In the long-term, this procedure allows the county to decrease its stores without sacrificing availability of parts.
CGL was involved early in the design process to help the county find life cycle savings that had positive annual and long-term impact on the cost of operations. Some suggestions were simple and easy to implement — use lower-cost and easier-to-maintain flooring in the jail and extend the warranties of building equipment — while other ideas required collaboration with all project stakeholders.
Specifically, CGL’s facility management professionals pushed for a single central plant for environmental control of both buildings. The original facility design called for space in each building to house local HVAC and plumbing equipment. Each building would have its own chillers, boilers and hot-water heaters as well as separate plumbing systems and cooling towers. Combining the equipment into one central plant had immediate construction savings, but those savings are overshadowed by the long-term compounded reduction in operational costs. Building one central plant allowed the county to install less equipment overall, but CGL helped specify cutting-edge equipment — in-series chillers, in this case — that will save the county millions in utility costs over the courthouse and justice center’s first 20 years of life.
The maintenance team’s experience with utility management was also used to the county’s benefit. The single-biggest savings measure came from the application of maintenance techniques used in other jail facilities, using processes unheard of by the building designer. The operations experts made sure the building’s electrical meters were aggregated with other county facilities to help establish a lower utility rate for the entire campus, saving more than $178,000 in utility costs every year.
All told, the influence of CGL’s operations experience during design and construction of the Forsyth County Courthouse and Justice Center will save the county more than $22.6 million over 20 years, and provide continuous and sustainable operations throughout the life of the facilities.
These examples for Forsyth County are scalable to every project that can be undertaken in individual facilities. Whenever new construction occurs, there is an opportunity for maintenance experts, whether contractors or in-house, to apply their knowledge and ability to affect long-term cost savings. Even small renovation projects may be an opportunity to upgrade utilities or make environmental controls more efficient. Maintenance personnel must assert themselves early in the design and construction process to have long-term cost impact on the buildings they oversee.
***
This article originally appeared in the March/April 2017 issue of Correctional News Magazine.